Reel holder:
According to customer needs, it can be made into fixed type or flip type.
According to customer site space requirements, it can be made into two rows, three rows or four rows, six rows
thread, etc.
Equipped with contact-type broken wire automatic stop device.
Equipped with six-ring tensioner (special shape can be customized)
Can be equipped with static elimination device (customer option)
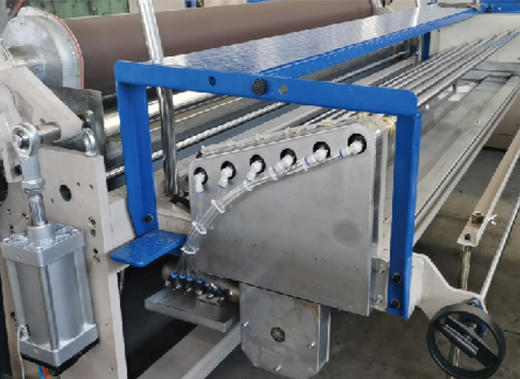
Condensing parts:
· Adopt 6 wet stratified sticks (condensation sticks) structure to protect the serosa.
· It can be equipped with a chiller (customer option) to achieve better dew condensation effect.
· Equipped with layered wheel frame lifting device.
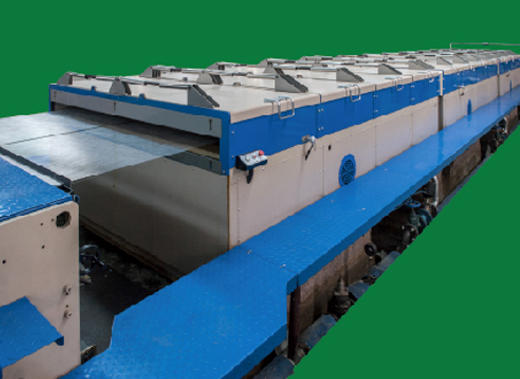
Dry parts:
· Adopt two-type reverse hot air circulation structure oven and five cylinder drying method.
· Each drying cylinder and drying room are equipped with independent temperature measurement and control system.
· Adopt tension sensor control system to ensure stable tension during operation.
· Equipped with an oiling device after drying the silk, and the speed of the oiling roller can be adjusted steplessly within a certain range.
· The cooling system of the drying wire can be selected as required (customer option).
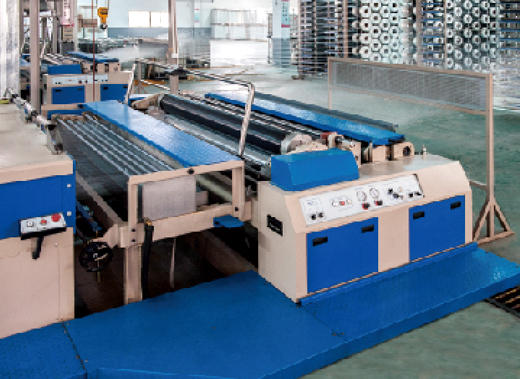
Sizing parts:
· Using the advanced double frequency conversion motor drive system, the wire tension between the sizing roll and the wire feed roll can be adjusted as required.
· Pneumatic dipping and grouting method and specially designed grouting rollers ensure uniform grouting at both ends and the middle of the filament.
· Equipped with pressing roller lifting lock and dipping roller lifting system, which makes cleaning and replacement of rollers more convenient, and can protect the rubber rollers during long-term downtime.
· Equipped with double-layer thermal insulation slurry bucket and slurry heating control circulation device.
· Equipped with automatic pulping device (optional).
· The newly designed slurry tank can effectively prevent slurry from splashing.
· Equipped with a box moving up and down, left and right, to fully extend the service life of the chopper.
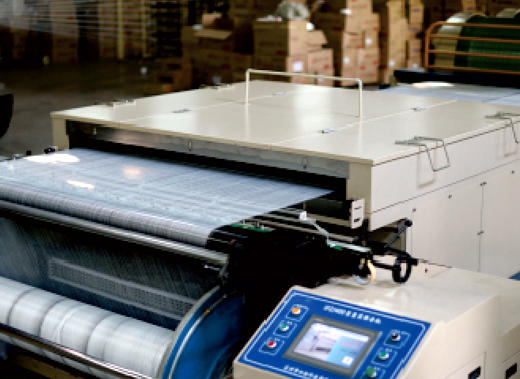
Cold air box parts (optional):
· When the oiled (wax) yarn passes through the cold air, the oil (wax) on the yarn can be cooled and solidified, and the yarn on the warp beam can also be cooled.

Coil part:
· Adopt hard alumina roller.
· Equipped with a wire pressing device to ensure that the wire is kept in tension when changing shafts.
· Equipped with tape sticking device.
· Pneumatic upper and lower shafts and flap opening and closing are used, and are equipped with air pressure sensors to ensure safety.
· Equipped with manual telescopic left and right movement and retractable expansion device. Equipped with telescopic Weng swing device, equipped with wire lifting device.
Can be equipped with static eliminator (customer option)
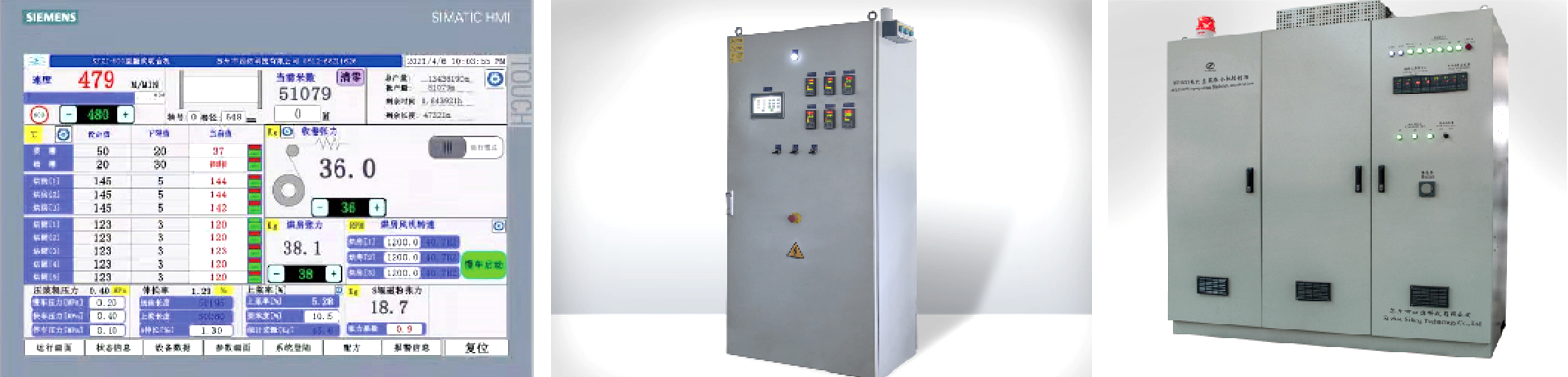
Control parts:
· Adopt advanced PLC control system and frequency conversion control mode to ensure operation under constant line speed and constant tension.
· Using touch screen control, the display is clearer and the operation is more convenient. ·Multi-camera control buttons to ensure convenient, safe and reliable use.