Introduction to Filament Weaving Preparation Equipment: Enhancing Efficiency and Quality in Textile Production
One of the primary functions of filament weaving preparation equipment is filament winding. This process involves transferring the filaments from individual bobbins onto a larger package called a warp beam. Filament winding machines are equipped with multiple winding stations that allow for the simultaneous winding of several filaments, enhancing productivity. These machines ensure uniform tension, alignment, and layering of the filaments, resulting in consistent and even distribution on the warp beam. Efficient filament winding is crucial as it lays the foundation for a smooth and successful weaving process.
Another essential task performed by filament weaving preparation equipment is warping. Warping involves the precise arrangement of filaments in a parallel configuration, ready to be transferred to the weaving loom. Warping machines allow for accurate length measurement and alignment of the filaments, ensuring that they are positioned correctly for weaving. These machines employ tension control systems and advanced sensors to maintain uniform tension throughout the warping process, minimizing the risk of yarn breakage or irregularities.
Filament beaming is another key step in the preparation process. Beaming machines transfer the filaments from the warp beam onto a beam that will be placed on the weaving loom. These machines ensure the smooth and controlled transfer of filaments, preventing tangling, slippage, or damage. The precise winding and beaming of filaments are critical for achieving consistent tension and positioning during the weaving process, which ultimately affects the quality and appearance of the finished fabric.
Sizing is an additional task performed by filament weaving preparation equipment. Sizing involves the application of a protective coating, called sizing, to the filaments before weaving. Sizing machines apply the sizing agent evenly to the filaments, which helps improve their handling properties, reduce friction, and enhance their resistance to abrasion during the weaving process. The sizing process contributes to the overall strength, integrity, and performance of the woven fabric.
modern filament weaving preparation equipment is equipped with advanced automation features and quality control mechanisms. Computerized control systems enable precise control over various parameters such as tension, speed, and positioning, ensuring consistent and accurate results. These machines are equipped with sensors and monitoring devices that detect and rectify any deviations or abnormalities during the preparation process. This level of automation and quality control enhances efficiency, minimizes human error, and ensures the production of high-quality fabrics.
The use of filament weaving preparation equipment not only improves efficiency but also offers flexibility in terms of fabric design and production. These machines are capable of handling a wide range of filament types, including natural fibers, synthetic fibers, and specialty yarns. They can accommodate different yarn counts, widths, and patterns, allowing textile manufacturers to produce a variety of fabrics, from lightweight and delicate materials to heavy-duty industrial textiles. The versatility and customization options provided by filament weaving preparation equipment contribute to the adaptability of textile mills to meet diverse market demands.
Another essential task performed by filament weaving preparation equipment is warping. Warping involves the precise arrangement of filaments in a parallel configuration, ready to be transferred to the weaving loom. Warping machines allow for accurate length measurement and alignment of the filaments, ensuring that they are positioned correctly for weaving. These machines employ tension control systems and advanced sensors to maintain uniform tension throughout the warping process, minimizing the risk of yarn breakage or irregularities.
Filament beaming is another key step in the preparation process. Beaming machines transfer the filaments from the warp beam onto a beam that will be placed on the weaving loom. These machines ensure the smooth and controlled transfer of filaments, preventing tangling, slippage, or damage. The precise winding and beaming of filaments are critical for achieving consistent tension and positioning during the weaving process, which ultimately affects the quality and appearance of the finished fabric.
Sizing is an additional task performed by filament weaving preparation equipment. Sizing involves the application of a protective coating, called sizing, to the filaments before weaving. Sizing machines apply the sizing agent evenly to the filaments, which helps improve their handling properties, reduce friction, and enhance their resistance to abrasion during the weaving process. The sizing process contributes to the overall strength, integrity, and performance of the woven fabric.
modern filament weaving preparation equipment is equipped with advanced automation features and quality control mechanisms. Computerized control systems enable precise control over various parameters such as tension, speed, and positioning, ensuring consistent and accurate results. These machines are equipped with sensors and monitoring devices that detect and rectify any deviations or abnormalities during the preparation process. This level of automation and quality control enhances efficiency, minimizes human error, and ensures the production of high-quality fabrics.
The use of filament weaving preparation equipment not only improves efficiency but also offers flexibility in terms of fabric design and production. These machines are capable of handling a wide range of filament types, including natural fibers, synthetic fibers, and specialty yarns. They can accommodate different yarn counts, widths, and patterns, allowing textile manufacturers to produce a variety of fabrics, from lightweight and delicate materials to heavy-duty industrial textiles. The versatility and customization options provided by filament weaving preparation equipment contribute to the adaptability of textile mills to meet diverse market demands.
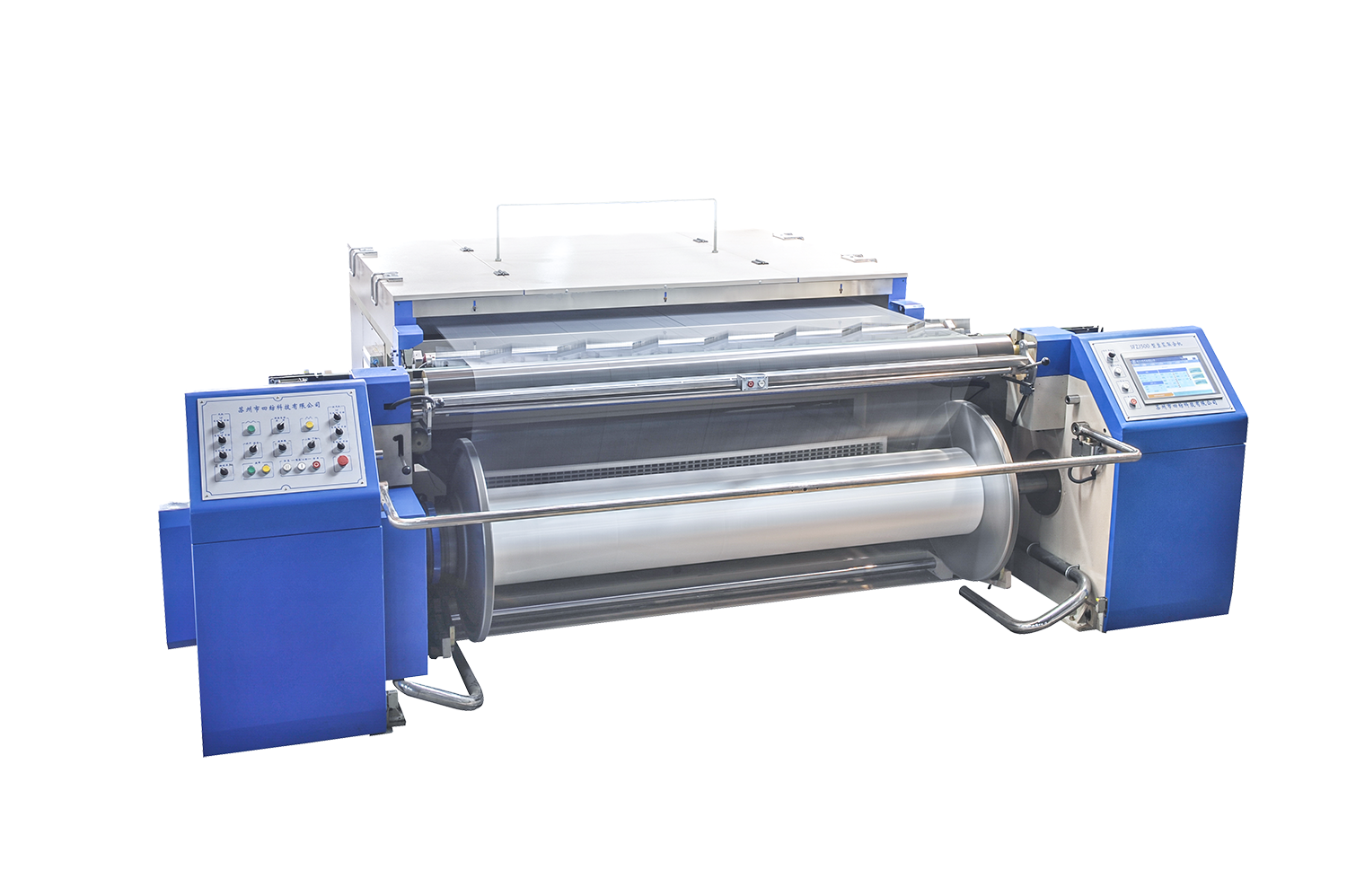